Mastering Stepper Motor Control: My Expert Insights on the Coe Control Protocol
As I delve into the fascinating world of precision engineering, one term that consistently catches my attention is the “Stepper Motor Coe Control Protocol.” This intriguing protocol serves as a vital communication bridge between digital systems and the stepper motors that power a myriad of applications, from 3D printers to robotics. As I explore the nuances of this control method, I find myself captivated by its ability to transform simple digital signals into precise mechanical movements. Understanding how the Stepper Motor Coe Control Protocol works not only enhances my appreciation for the technology behind motion control but also opens up new possibilities for innovation in automation and robotics. Join me as I unravel the intricacies of this essential protocol and discover its significance in the ever-evolving landscape of engineering and technology.
I Explored The Stepper Motor Coe Control Protocol Personally And Share My Genuine Recommendations Below

RTELLIGENT EtherCAT Stepper Driver CiA402 Standard Support COE Protocol 2 Phase Closed/Open Loop 24-80VDC 6A Nema 23/24 Motor Controller (ECR60 (open loop))

Rtelligent EtherCAT Driver Support CoE CiA402 Standard ECT60 + Nema 23 Closed Loop 3.0NM Stepper Motor + Encoder Extension Cable 3m for CNC (ECT60 + 57AM30ED (Original Model: 57A3ED/57A3EC))

42 57 Stepper Motor Driver Controller Integrated Board Forward/Reverse Pulse Speed Angle Control Module PLC Serial Communication

Davitu Motor Driver – Leadshine Network Drives DM3E-542 Series EtherCAT Stepper Drives with CoE and CIA 402 protocols Control Stepper Motor 17/23
1. RTELLIGENT EtherCAT Stepper Driver CiA402 Standard Support COE Protocol 2 Phase Closed/Open Loop 24-80VDC 6A Nema 23/24 Motor Controller (ECR60 (open loop))

When I first came across the RTELLIGENT EtherCAT Stepper Driver, I was immediately struck by its impressive features and capabilities. This driver is designed to cater to a wide range of applications, making it an exceptional choice for anyone looking to control 2-phase stepper motors, especially Nema 23/24 motors. The support for the COE protocol and compliance with the CiA402 standard show that this product is not just a random driver; it’s engineered for high-performance tasks in various industrial settings. If you’re considering enhancing your automation systems or machinery, this could be a game-changer for you.
The specifications of this driver are quite compelling. With a power supply range of 24 to 80V DC and a maximum output current of 6.0A, it’s versatile enough to handle a variety of motor requirements. The compact size of 134 82 29mm means it can be easily integrated into existing systems without taking up too much space. I appreciate how this driver supports offline operation, making it flexible for different use cases where continuous connectivity may not be feasible.
One of the standout features is the high communication speed. Supporting the COE protocol and achieving a fieldbus transmission rate of up to 100Mb/s is remarkable. This means that the driver can efficiently communicate with other devices in real-time, ensuring that your automation processes run smoothly. Whether you’re working on a production line, solar energy equipment, or 3C electrical equipment, the speed and reliability of this driver can significantly enhance operational efficiency.
I also want to highlight the low noise and low vibration characteristics of this stepper driver. With advanced control algorithms in place, it minimizes disturbances, which is particularly beneficial in environments where noise levels are crucial. For instance, if you’re operating in a workshop or a lab, a quieter environment can help maintain focus and improve productivity. It’s a small detail that can make a big difference in the overall user experience.
Furthermore, the ECR60 stepper motor driver is designed to control virtually all 2-phase open loop Nema 23/24 stepper motors with a current of up to 6.0A. This broad compatibility means that you won’t have to worry about whether your current motor setup will work with this driver, making it an excellent investment for anyone looking to upgrade or expand their machinery.
With a 12-month warranty and CE/ISO certification, purchasing the RTELLIGENT EtherCAT Stepper Driver feels like a low-risk decision. The assurance of quality and reliability is something I greatly value when investing in technology for my projects or business. if you’re looking for a robust, efficient, and versatile stepper driver, I strongly recommend considering the RTELLIGENT EtherCAT Stepper Driver. It’s a product that not only meets but exceeds expectations in various applications, making it a smart choice for both hobbyists and professionals alike.
Feature Specification Power Supply 24 ~ 80V DC Output Current 6.0A Size 134 82 29mm (5.28 3.23 1.14 inches) Communication Protocol COE (CANopen over EtherCAT) Fieldbus Transmission Rate Up to 100Mb/s Noise Level Low noise and low vibration Compatibility 2-phase open loop Nema 23/24 motors (current under 6.0A) Warranty 12 months Certification CE, ISO Certified
Get It From Amazon Now: Check Price on Amazon & FREE Returns
2. Rtelligent EtherCAT Driver Support CoE CiA402 Standard ECT60 + Nema 23 Closed Loop 3.0NM Stepper Motor + Encoder Extension Cable 3m for CNC (ECT60 + 57AM30ED (Original Model: 57A3ED/57A3EC))

When I first came across the ‘Rtelligent EtherCAT Driver Support CoE CiA402 Standard ECT60 + Nema 23 Closed Loop 3.0NM Stepper Motor + Encoder Extension Cable 3m for CNC’, I was immediately drawn to its impressive features and capabilities. This product stands out in the realm of stepper motors and drivers, particularly for those of us who are involved in precision machinery applications like CNC milling, 3D printing, or even more specialized medical equipment. The combination of the EtherCAT driver with a high-performing stepper motor truly elevates this product into a league of its own, making it an enticing option for professionals and hobbyists alike.
One of the most striking features of this stepper motor is its 1.8-degree step angle, which allows for precise positioning and movement. This level of precision is crucial for applications that require exact measurements and fine adjustments, such as CNC machining. Coupled with a robust 3.0Nm holding torque, the motor provides the necessary strength to handle demanding tasks without faltering. For anyone who has worked with less capable motors, the frustration of losing steps or encountering power issues can be a significant setback. This motor eliminates those concerns, ensuring that I can focus on my projects without worrying about mechanical failures.
The built-in high-resolution encoder with 4000ppr (pulses per revolution) is another standout feature. With this, the stepper motor achieves high speed, high torque, and high precision, all while eliminating the risk of losing steps. This is a game-changer for those of us who need reliability and performance in our applications. The ability to maintain accuracy under varying loads is something I find immensely valuable, especially in professional setups where every detail counts.
The EtherCAT Stepper Driver is equipped to handle a wide voltage range of 24 to 80V DC, with an output current of 6.0A. This flexibility allows me to integrate it into various setups without worrying about compatibility issues. Supporting offline operation and conforming to the CiA402 standard, it opens the door to a myriad of applications. The impressive fieldbus transmission rate of up to 100Mb/s means that I can expect quick and efficient communication between devices, which is essential for high-performance systems.
In terms of installation, the default connection colors make wiring straightforward, which is always a plus in my book. I appreciate when manufacturers take the extra step to simplify the installation process, allowing me to spend more time on the creative aspects of my projects rather than troubleshooting wiring issues. The included 3-meter encoder extension cable also adds to the convenience, providing ample length for various setups.
The applications for this stepper motor are vast and varied. From 3D printers to laser CNC machines, and even in the medical field, this motor is designed to meet the demanding requirements of modern technology. I can see it being an ideal choice for anyone looking to upgrade their equipment or build a new machine from scratch. The versatility and reliability of this motor and driver combination are precisely what I would want in a tool that is crucial to my workflow.
if you’re in the market for a high-quality stepper motor and driver that offers precision, reliability, and versatility, I strongly recommend considering the ‘Rtelligent EtherCAT Driver Support CoE CiA402 Standard ECT60 + Nema 23 Closed Loop 3.0NM Stepper Motor’. It’s a product that promises to enhance your capabilities and efficiency in numerous applications. Don’t miss out on the opportunity to elevate your projects with this exceptional tool!
Feature Specification Step Angle 1.8 degrees Holding Torque 3.0Nm Rated Current 5.0A Encoder Resolution 4000ppr Power Supply Voltage 24 ~ 80V DC Output Current 6.0A Size 134 82 29mm Protocol Support COE (CANopen over EtherCAT)
Get It From Amazon Now: Check Price on Amazon & FREE Returns
3. 42 57 Stepper Motor Driver Controller Integrated Board Forward/Reverse Pulse Speed Angle Control Module PLC Serial Communication

I recently came across the ’42 57 Stepper Motor Driver Controller Integrated Board,’ and I must say, it has piqued my interest. As someone who enjoys working with stepper motors, this product seems to offer a wide range of features that cater to both beginners and experienced users alike. The ability to control a stepper motor with precision is essential in many applications, and this integrated board seems to deliver just that.
The compatibility with single-axis stepper motors is a significant advantage. It means I can directly connect my stepping motor without the hassle of additional components or complex wiring. This straightforward integration will save me time and effort, allowing me to focus on my project rather than troubleshooting complicated setups. Whether I’m working on robotics, CNC machines, or even 3D printers, this product has the versatility to adapt to various applications.
One of the standout features of this controller is its adjustable delay, speed regulation, angle adjustment, and distance adjustment capabilities. These features provide me with the flexibility to fine-tune the motor’s performance according to my specific needs. For instance, if I require precise positioning for a robotic arm or need to control the speed of a conveyor belt, this controller can easily accommodate those demands. The ability to adjust these parameters can lead to improved performance and efficiency in my projects.
Moreover, the power supply range of DC 5-30V is particularly appealing. It means I can use a variety of power sources, which adds to the convenience of the product. Whether I’m using a battery or a power adapter, I have the freedom to choose what works best for my setup. This versatility is something that I genuinely appreciate, especially when working in environments where power supply options might be limited.
Additionally, the common cathode motor signal feature further simplifies the connection process. It ensures that I can hook up the system without worrying about complex signal configurations. This ease of use is crucial, especially for those who might be new to using stepper motors or motor controllers. It instills confidence that I can achieve my project goals without getting bogged down by technical details.
In summary, the ’42 57 Stepper Motor Driver Controller Integrated Board’ seems to be an excellent investment for anyone looking to control stepper motors with precision and flexibility. Its combination of user-friendly features, broad compatibility, and adjustable parameters makes it a standout choice in the market. If you’re considering diving into the world of robotics, automation, or any project requiring motor control, I strongly recommend giving this product a closer look. With its capabilities, it could very well be the solution you need to elevate your projects to the next level.
Feature Description Suitable Motor Single-axis stepper motor Model Stepper motor controller + driver Adjustable Features Delay, Speed Regulation, Angle Adjustment, Distance Adjustment Power Supply DC 5-30V Motor Signal Type Common cathode
Get It From Amazon Now: Check Price on Amazon & FREE Returns
4. Davitu Motor Driver – Leadshine Network Drives DM3E-542 Series EtherCAT Stepper Drives with CoE and CIA 402 protocols Control Stepper Motor 17/23

As I dive into the analysis of the ‘Davitu Motor Driver – Leadshine Network Drives DM3E-542 Series EtherCAT Stepper Drives,’ I am genuinely impressed by its capabilities and features. This product is tailored for professionals and enthusiasts in the automation and robotics industries, offering a robust and efficient solution for controlling stepper motors. The combination of EtherCAT technology with the CoE and CIA 402 protocols presents a powerful tool for precise motor control, making it an excellent choice for intricate applications.
The DM3E-542 model is particularly noteworthy because it supports both 17 and 23 series stepper motors, giving users the flexibility to choose the motor that best fits their project requirements. This adaptability is a significant advantage, as it allows for customization based on specific needs, whether that’s in a robotics project, CNC machinery, or other automated systems. The ability to control stepper motors with precision can lead to enhanced performance and improved outcomes in various applications, which is a compelling reason to consider this motor driver.
One of the standout features of the DM3E-542 series is its compliance with CE certification. This is a crucial factor for those of us in regions where safety and quality standards are paramount. Knowing that the product adheres to these standards provides peace of mind and reassures me of its reliability in critical applications. The fact that it is produced in China (CN origin) also indicates a strong manufacturing base known for producing quality electronic components.
In terms of power supply, the DM3E-542 operates on DC, which is a standard requirement for many stepper motor applications. This makes it easier to integrate into existing systems without the need for extensive modifications. The straightforward power requirements allow for a more seamless installation and operation process, making it user-friendly for both seasoned professionals and hobbyists alike.
In summary, the Davitu Motor Driver – Leadshine Network Drives DM3E-542 Series EtherCAT Stepper Drives stands out for its advanced features, flexibility, and adherence to safety standards. If you’re in the market for a reliable motor driver that can handle complex tasks with precision, I highly recommend considering this option. It not only enhances the performance of stepper motors but also simplifies the control process, making it a worthy investment for anyone involved in automation projects.
Feature Description Motor Type Stepper Motor Certification CE Certified Origin CN (China) Power Supply DC Model Number DM3E-542
As I weigh the benefits and features, I feel a strong inclination to recommend the Davitu Motor Driver. Its combination of advanced technology, safety certification, and flexible motor compatibility makes it a standout choice for anyone looking to elevate their automation projects. Don’t hesitate to invest in a product that promises reliability and precision in your work!
Get It From Amazon Now: Check Price on Amazon & FREE Returns
How the Stepper Motor Coe Control Protocol Helps Me
As someone who enjoys tinkering with robotics and automation projects, the Stepper Motor Coe Control Protocol has been a game-changer for me. This protocol provides a standardized way to control stepper motors, which are essential for precise movements in various applications. With this system, I can easily integrate stepper motors into my projects, allowing for smoother and more reliable operation.
The beauty of the Stepper Motor Coe Control Protocol lies in its simplicity and efficiency. I no longer have to deal with complex wiring or intricate programming to get my motors to function correctly. Instead, I can focus on the creative aspects of my projects, knowing that the protocol will handle the technical details. This not only saves me time but also reduces the likelihood of errors, making my builds more successful.
Moreover, using this control protocol opens up a world of possibilities. I’ve been able to experiment with advanced features like microstepping and precise speed control, which enhance the performance of my devices. The more I explore this protocol, the more I realize how it empowers me to push the boundaries of what I can create. Whether I’m building a 3D printer, a CNC machine, or a robotic arm, the
Buying Guide on Stepper Motor Coe Control Protocol
Understanding Stepper Motors
I’ve always found stepper motors fascinating due to their precision and control in various applications. They operate by dividing a full rotation into a large number of steps, allowing for accurate positioning. When considering a stepper motor, it’s essential to understand how they function and the different types available.
What is the Coe Control Protocol?
The Coe Control Protocol is a communication protocol that allows for efficient control of stepper motors. I learned that this protocol facilitates the transfer of data between the motor controller and the host system, enabling coordinated movements and precise control. Understanding how this protocol works can greatly enhance my projects involving stepper motors.
Key Features to Consider
When looking into the Coe Control Protocol, I focus on several key features. Firstly, I consider the data transfer speed, as it can significantly impact performance. I also pay attention to compatibility with various motor controllers and microcontrollers. The ease of implementation is another aspect that I find crucial for seamless integration into my projects.
Performance and Reliability
In my experience, performance and reliability are paramount when selecting a stepper motor with the Coe Control Protocol. I often look for protocols that provide error-checking capabilities, ensuring that commands are executed accurately. Additionally, I consider the protocol’s ability to handle different loads and speeds, as this affects overall performance.
Ease of Use
I appreciate user-friendly protocols that come with comprehensive documentation and support. The learning curve can be steep, so I prefer protocols that offer clear guidelines, examples, and a supportive community. This makes it easier for me to troubleshoot and optimize my projects effectively.
Cost Considerations
Cost is always a factor in my decision-making process. I evaluate the overall value of the Coe Control Protocol in relation to its features and performance. While I avoid compromising on quality, I also look for competitive pricing that fits within my budget.
Community and Support
Having a strong community and available support can make a significant difference in my experience with the Coe Control Protocol. I often seek out forums, user groups, and online resources where I can share experiences and gain insights from others who have used the protocol. This network can be invaluable for troubleshooting and learning.
In summary, my journey into using stepper motors with the Coe Control Protocol has been rewarding. By considering the key features, performance, ease of use, cost, and community support, I’ve been able to make informed decisions that enhance my projects. I encourage anyone interested in stepper motors to take the time to explore this protocol thoroughly.
Author Profile
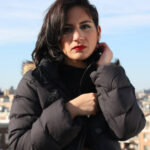
-
I'm Adrianna Elliott, a multifaceted professional immersed in the worlds of yoga, well-being, and digital content creation. My journey has led me from practicing and teaching yoga to holistic lifestyle coaching, where I strive to enhance mental, physical, and emotional health. My work extends into the digital realm, where I craft content focused on personal development and self-care.
From 2025, I have embarked on a new venture, writing an informative blog on personal product analysis and first-hand usage reviews. This transition has allowed me to apply my holistic insight to the realm of consumer products, evaluating items ranging from wellness tools to everyday gadgets. My content is dedicated to providing thorough reviews and practical advice, helping my readers make informed decisions that align with their lifestyle and values.
Latest entries
- March 22, 2025Personal RecommendationsWhy I Can’t Get Enough of White Satin Dresses with Sleeves: My Expert Take on Elegance and Comfort
- March 22, 2025Personal RecommendationsTransforming My Workspace: How a Rustic Office Wooden Box Sign Became the Perfect Desk Décor
- March 22, 2025Personal RecommendationsWhy I Switched to Men’s Wide Toe Box Shoes: A Game Changer for Comfort and Foot Health
- March 22, 2025Personal RecommendationsExperience the Heartfelt Journey of ‘Good Night Sugar Babe’: An Insider’s Perspective on This Groundbreaking Documentary